1. Always warm up the spindle by running at low speed for few minutes, if it has been idle for an extended time.
2. Check spindle’s run-out every six months and/or after any crash using a calibrated spindle test bar. Also, monitor the spindle’s drawbar spring force with a pull force test. Pull force should be at least 80% of the designed value and a sizable drop in force could lead to excessive vibration and run-out, which can damage the spindle and tool holder. Fretting corrosion can appear on the taper and the finished part’s surface.
3. While grease-bearing spindles are factory lubricated for life, many of today’s machines are equipped with oil-air lubricated bearing spindles. In addition to keeping up with oil levels on these machines, workshops are advised to monitor the air-intake filters on a regular basis as well. Operations personnel should keep an eye on any leaks or pressure drops in the air/oil lines.
4. Keep the coolant (for the cutting tool), directed at the actual cut as much as possible to eliminate (or at least reduce) potential backsplash to the spindle.
5. On high-speed spindles, shops must ensure the spindle chiller units are always operating properly. A good indicator of a potential spindle problem is any rise in chiller system output temperature. Ignoring this will cause spindle failure.
6. Here are some more tips very specific to milling spindles:
- Keep the spindle taper dry and clean. The taper on a typical milling spindle sometimes may allow material being machined to get caught between the tool and the taper interface. This can result in damage both to the spindle and the tool holder.
- It’s crucial to maintain proper ATC alignment. If the ATC does not insert the tool holder perfectly, damage to the spindle and tool holder may result.
- Always use balanced tool holders, especially on high-speed machines, to avoid vibration and unbalanced load/forces affecting the spindle bearings.
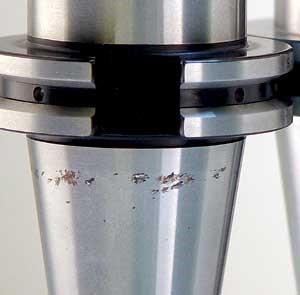
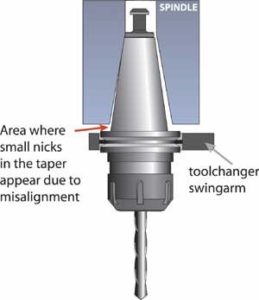
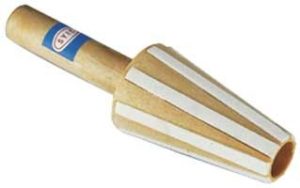